Getting your Trinity Audio player ready...
|
Kay Scheffler explores recent advances in optical microscopy that could significantly improve manufacturing
For manufacturers and component suppliers in the automotive industry, technical cleanliness is an important topic. The ability to analyse technical cleanliness rapidly, accurately, and reliably over the entire workflow is a significant advantage. But what exactly is meant by the term “technical cleanliness”? It concerns the fabrication of parts and components which are sensitive to contamination, the presence of which can cause a significant decrease in performance. In the automotive industry, cleanliness analysis is performed with optical microscopy. Particle counting and analysis is done to ensure that manufactured parts and components have an acceptable level of cleanliness, making it a critical part of quality assurance.
Automakers incorporate cleanliness workflows in their production lines to ensure they comply with technical cleanliness guidelines and standards established by international and regional organisations like the VDA (German Association of the Automotive Industry) and ISO (International Organization for Standardization). Maintaining the highest quality control standards helps ensure that the many components that go into every vehicle will work efficiently and harmoniously, improving long-term vehicle performance and lifetime.
Analysing and maintaining cleanliness in vehicle manufacturing is far from easy because it has traditionally required tools and services provided by multiple vendors that do not always work seamlessly together, but, fortunately, this is changing. New integrated solutions—driven by advanced-microscopy technology—are making it easier to analyse and maintain clean environments.
Determining particle cleanliness
The cleanliness standards and guidelines that most automakers follow are spelled out in ISO 16232 and VDA 19. These standards provide the industry’s accepted definitions and ranges for the size and composition of particles that are the most threatening, the threshold values for particle identification, and other key parameters used in cleanliness analysis. ISO 16232 defines methods for determining the size and number of contaminant particles, while VDA 19 details such factors as how to select the ideal inspection method, appropriate methods for clean handling of test components, and techniques for setting up extraction procedures.
Understanding particle composition is particularly important for automakers because it allows them to not only determine a particle’s potential to cause damage, but also to identify the source of contamination. And with the rapid growth of the electric vehicle (EV) market, now is the ideal time to embrace new, integrated tools and services for analysing and optimising cleanliness. That is because the growth of the EV market has increased the use of electronic components which must also comply with cleanliness guidelines.
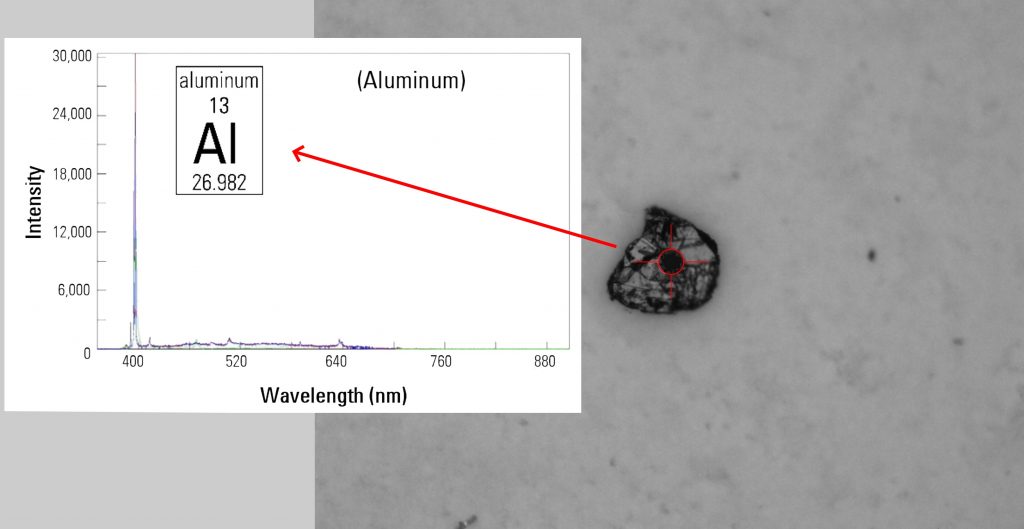
Microscopy aids analysis workflow
Contaminant particles are typically extracted from components by cleaning them with a special liquid. The run-off is then passed through a membrane filter which collects the particles on the surface. The particles are analysed using an optical microscope and image analysis techniques to determine the particle size distribution.
Now, new technology can help automakers streamline key steps in the cleanliness-analysis workflow. For example, after they filter parts and extract potential contaminants, they can improve the efficiency of composition analysis by using optical microscopes that combine visual and qualitative chemical inspection. This eliminates the need to transfer filters to another instrument or add sample-preparation steps, significantly cutting the time it takes to complete visual and chemical material analysis.
From there, automakers can use integrated microscopy and software automation for particle analysis. Understanding particle composition can be an advantage for reliably determining a particle’s potential to cause damage and identifying the source of contamination. With a two-methods-in-one materials analysis solution, combining optical microscopy and laser-induced breakdown spectroscopy (LIBS), a composition analysis of particles can be efficiently performed. The particles on a filter are visually examined and then immediately chemically analysed with LIBS without the need to transfer the filter to another instrument or additional sample preparation. This information can then be used to better assess the potential of the particles to cause damage.
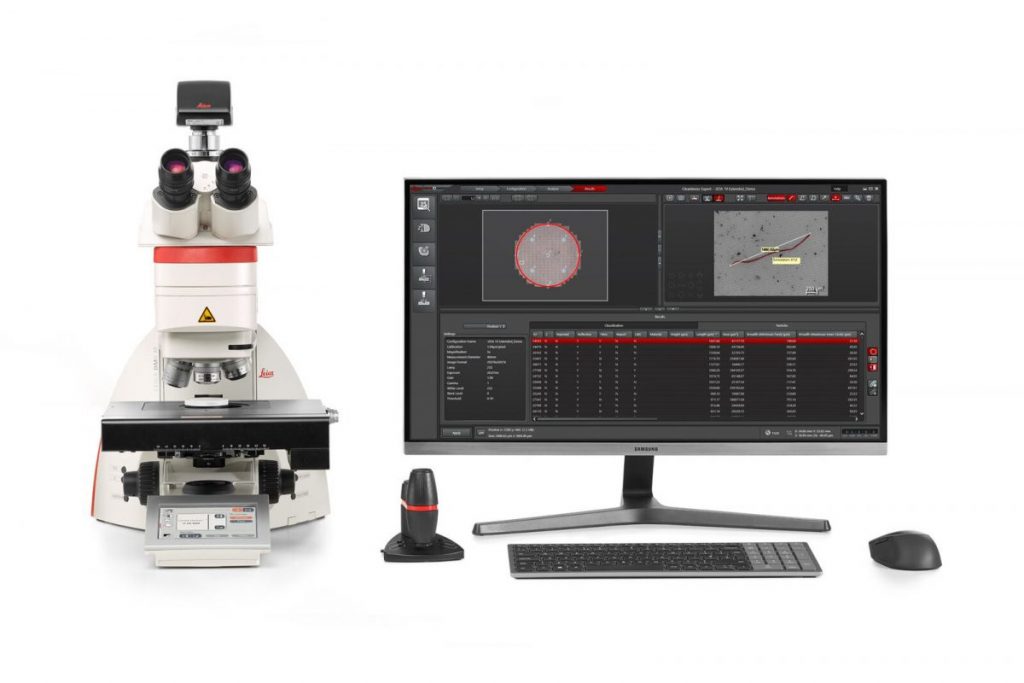
Advanced imaging maximises safety
Recent advances in imaging solutions are helping to further streamline cleanliness analysis. For example, reflective metal particles have a higher potential to cause damage than other particles. These potentially dangerous particles can influence the longevity of a component or even cause a system failure. Advanced imaging solutions can identify these killer metallic particles automatically. Then, once automakers complete that analysis, they can use integrated software solutions to automatically review the results against required industry standards.
The growth of the EV market has increased the use of electronic components which must also comply with cleanliness guidelines
By looking at the overall cleanliness-analysis workflow, automakers can work with vendors to establish step-by-step plans for optimising the workflow. With advanced automation, carmakers can improve the quality and speed by which they identify potential killer particles, pinpoint the source of the contamination, and eliminate the damaging particles.
Cleanliness analysis in the auto industry is a rapidly evolving field. Parts suppliers and vehicle manufacturers must work together to strengthen the guidelines around what needs to be measured to best predict potential damage from particulates. In the meantime, automakers can do their part to minimise contamination—and by extension, maximise performance—by continuously improving the procedures they use to guarantee a clean manufacturing workflow.
Gaining a competitive edge
With an integrated cleanliness-analysis solution provided by a trusted partner, automotive industry manufacturers should be able to easily meet the current requirements of ISO 16232 and VDA 19 and be covered for any future updates that may be introduced. The right solution will ensure that manufacturers do not only find the right option for their cleanliness-validation needs, but that they can ultimately gain a competitive advantage by streamlining their workflow.
About the author: Kay Scheffler is Product Manager, Applied Microscopy, at Leica Microsystems